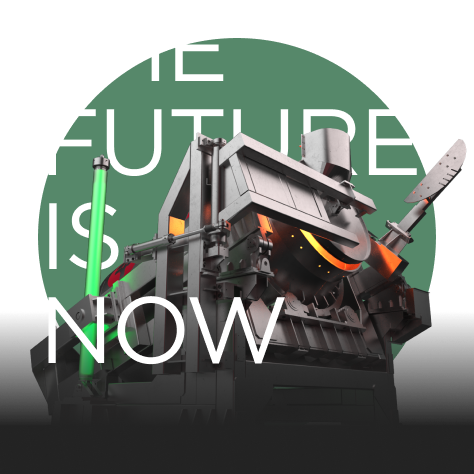
Fueling a sustainable future through the art of design and innovation.
GHI are committed to achieving a carbon neutral footprint by 2050.
We are constantly leading projects in the decarbonization of the industrial sector, replacing fossil fuels with clean and efficient energy sources like green hydrogen and renewable electricity.
Our energy-efficient equipment and resource optimization through digitalization are driving us towards a greener future. Join us in creating a sustainable world where the future truly is green.
How do we see the future of aluminium recycling?
ZERO WASTE PLANT
Our Smart Plants use clean and renewable energy to power an electrolyzer that produces hydrogen and oxygen. This electrolysis process is particularly suitable for scrap recycling in the tilting rotary furnace, as it utilizes both hydrogen and oxygen.
For post-consumer scrap recycling, tilting rotary furnaces and vortex furnaces with waste elimination systems will be fired with this low-carbon fuel. Hydrogen will replace natural gas. Maintenance and alloy furnaces will use renewable electricity as fuel for heating.
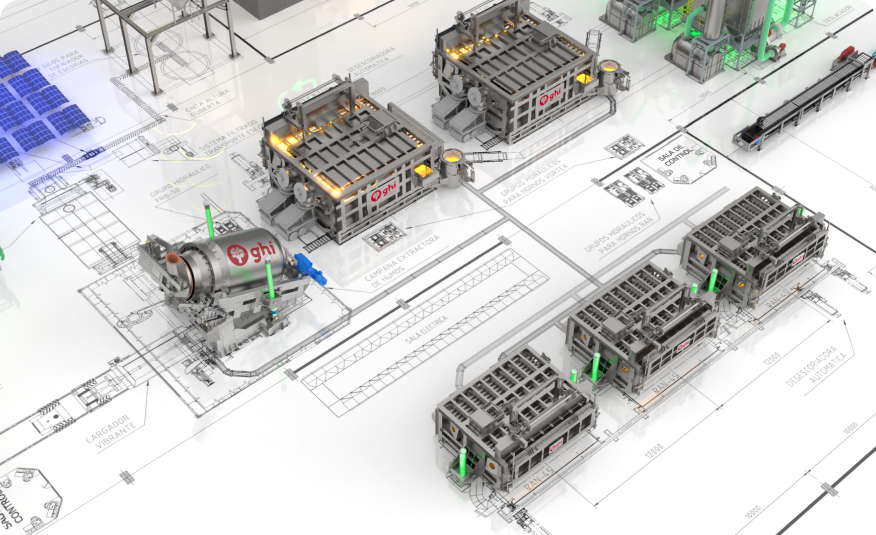
EMISSION FREE
The plant recycles and treats all by products, such as slag, salt cake, and generated fumes, to create circular plants without waste through sustainable methods of aluminium alloy production.
A slag cooler is used to increase aluminium recovery from slag, reduce oxidation and emissions, as well as space and cooling time. Sorting facilitates the recycling of salts by specialized companies and the use of pieces to fill roads.
Total circularity is the clear path to the future, and GHI Smart Furnaces is driving this change.
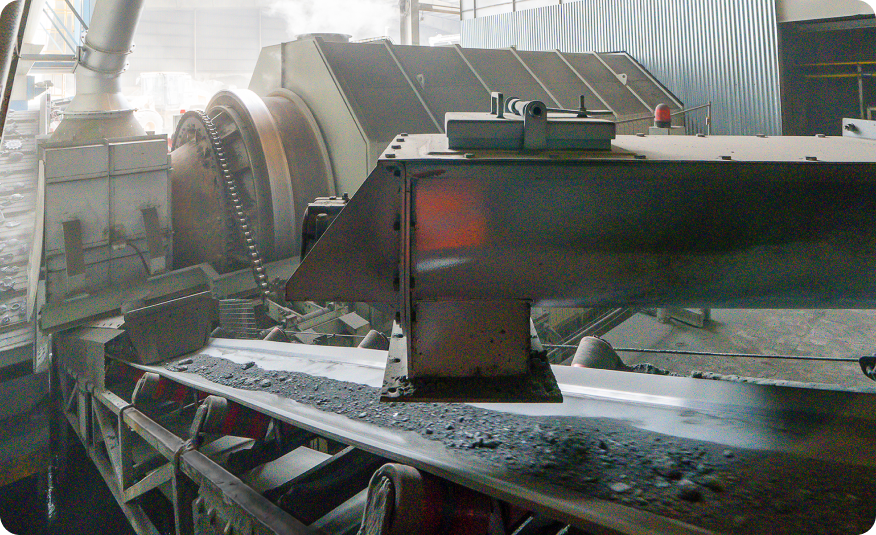
SMART TO BE PROFITABLE
The Plant of the Future utilizes Machine learning and Artificial intelligence to enhance foundry operations, employing our large industrial furnaces, which offer proven high economic performance.
The plant collects real-time data to optimize their processes and increase plant profitability through our digitalization and continuous improvement expertise.
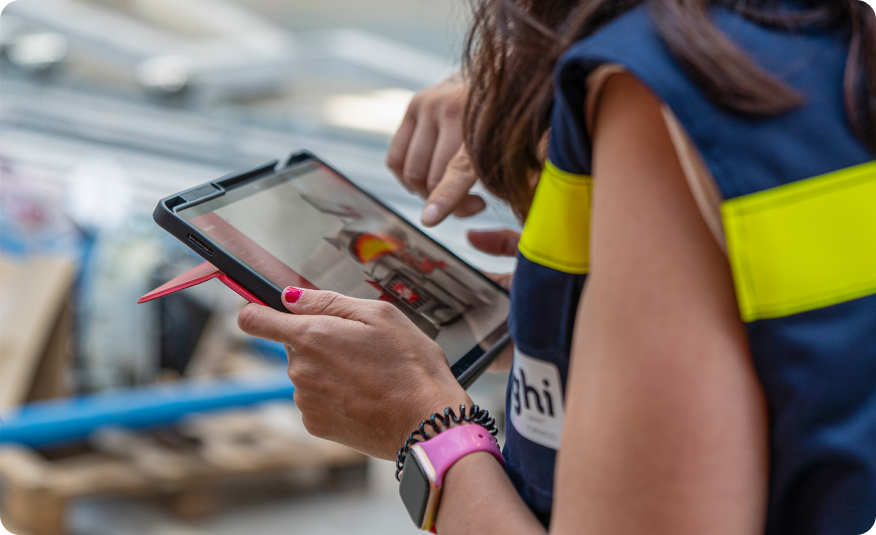
NEW TALENTS
The future plant demands hybrid job roles, merging technical metallurgy experts with cutting-edge skills in Big Data and Machine Learning.
These professionals will be able to explore the benefits of Artificial Intelligence, using these skills to predict and control the mechanical properties of aluminium alloys, discover new materials, and develop new alloys.
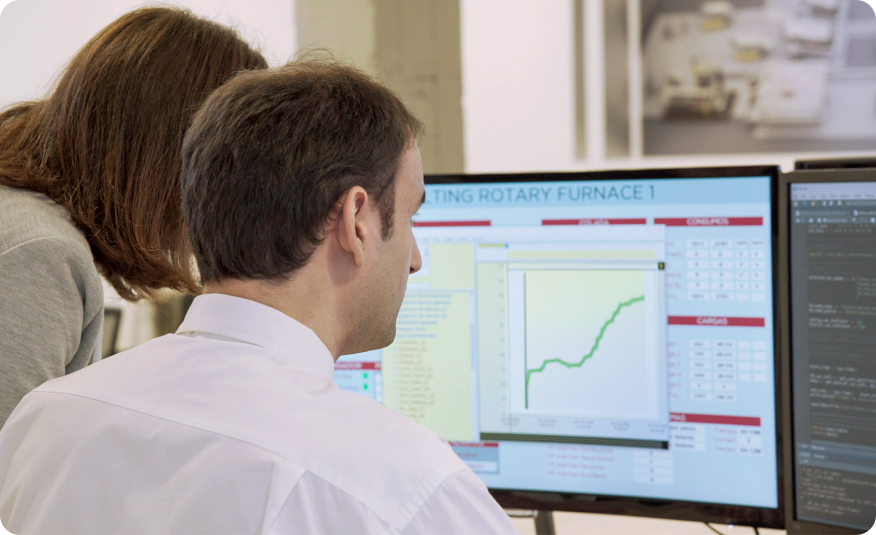
Meet our green projects, just coming out of the furnace.
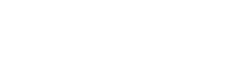
Designing, manufacturing, and testing intelligent burners for hydrogen/oxygen mixtures in metallurgical furnaces, using oxygen as a combustion agent. Our aim is to decarbonize industrial furnaces in steelmaking, foundry, forging, and heat treatment sectors, using "green hydrogen" as the sole fuel source.
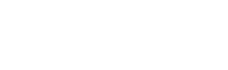
In collaboration with Europe through public and private partnerships, we are advancing the development of oxygas burners fueled by hydrogen, designed for implementation in pilot projects and industrial furnaces.
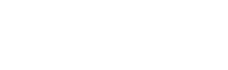
A national project to implement and validate new green hydrogen production and use methods, in addition to CO2 capture and deepening energy efficiency, integrating the result into intensive industry processes with the aim of advancing decarbonization.
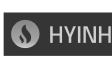
A joint European project for the integration of hydrogen in the entire value chain of aluminum and steel processes, from melting to heat treatment, implementing the technology in various furnaces.
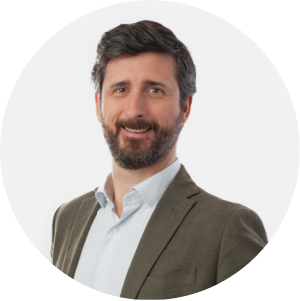
Let Iñigo Guinea help you today.
Iñigo Guinea, CEO, invites you to join us on the journey to decarbonize industries and explore our initiatives and be a part of the change. Contact Iñigo now to discover how, together, we can transform the future of aluminium recycling.